Implementation OF MES and ERP
Increased Efficiency of Resources’
Leading Strategic Growth and Profit
Manufacturing Execution Systems (MES) is a dynamic software solution that increases the overall profit margin of your manufacturing business by ensuring
- Optimum utilization of resources used for manufacturing and thus
- Increasing overall efficiency of production by
- Automizing all the processes involved and
-
Improved manufacturing reliability and product traceability with centralized processes and automated data collection
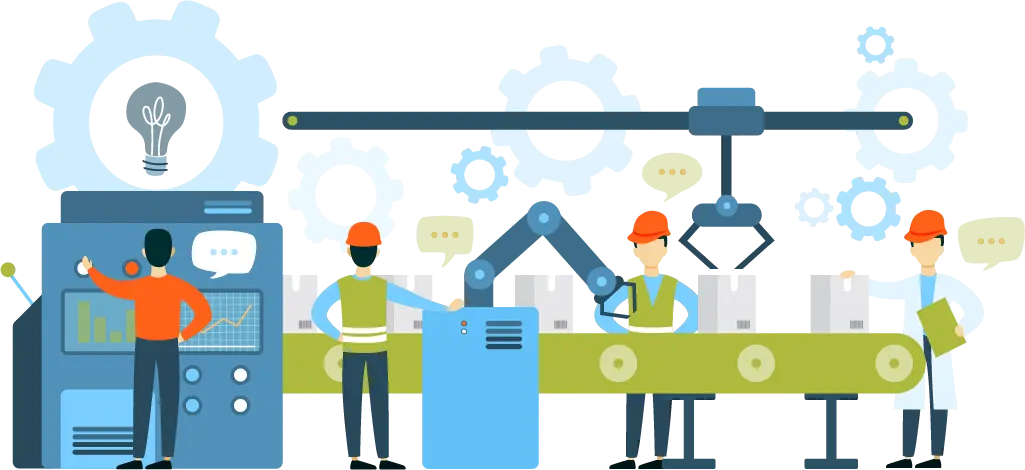
Monitoring, tracking, maintaining documentation, controlling, and synchronizing real-time complex manufacturing processes of products from raw materials to finished products by facilitating the easiest data flow between ERP and execution system.
MES creates an integrated ecosystem between automated Process Control systems and ERP, offering a holistic view of finance, procurement, supply chain management, and manufacturing logistics, along with quality management and increased production efficiency. Combining such information increases agility and provides robust data that improves forecasting on everything from sales to optimum asset utilization to manufacturing process management.
A Quick Round-up of Manufacturing Industry Challenges
- Keeping up with compliance regulations
- Lack of Process Integration
- Maximizing Utilization of Resources
- Scheduling work orders among workers
- Managing inventory
- Managing work centers
- Keeping Track Records of ongoing work orders
- Irregular Equipment maintenance/replacements
- Issues with work order flow
- Automize quality checks
- Unable to analyze the efficiency of workers
- Automizing product tracking and work orders linked
- Automizing product tracking and work orders linked
- Assortment and analysis of a large amount of data
Features
- Resource Allocation
- Operations scheduling
- Manage Equipment Allocation and Maintenance
- RFID-based Products Identification and Tracking
- Plant Management
- Process Management
- Quality Control and Rework Management
- Inventory Management
- Product Lifecycle Management for Bill Of Materials and Operation
- Maintenance Management with QC checklist
- SFTP-based SAP INTEGRATION
- Access level control of user’ work
- User Management
- Quick and Easy Reports and analysis
- Performance Analysis
- Alert and Notification
- Automated process for User Management
- Automated process for equipment Maintenance
Benefits
- Real-Time global monitoring and synchronization of manufacturing activities
- Optimized efficiency of Business Units, Plant, Work Station, and Work Centers
- Increased resource efficiency
- Improved Quality of products manufactured
- Ensure quality standards of products manufactured
- Custom workflow of workers & approvals at various levels
- Easy traceability of ongoing maintenance assistant
- Easiest Traceability of products manufactured
- Easiest time evaluation of Work Orders
- Improved security and accuracy through RFID tracking
- Reduced overall manufacturing lead time
- Increased Equipment Effectiveness
- Seamless Data Transfer
- Enhanced collaboration between work teams
-
Cost control by eliminating waste